The Difference Between Job Safety Analysis and Risk Assessment
Job safety analysis and risk assessment seem similar, since they’re both tools for reducing risk — but they’re not the same.
While the two do have some basic principles in common, mixing up job safety analysis with risk assessment is sort of like using a screwdriver to drive a nail. Or using a rake to shovel your driveway.
Even if you already perform both types of assessments for your organization, it’s worth reviewing the differences. This will help you make sure you’re not inadvertently creating more work for yourself.
Definition of job safety analysis and risk assessment
Before we get into the differences of these processes, let’s define what we’re talking about:
Job safety analysis: A formal process to identify the dangers of specific job tasks in order to reduce the risk of injury to workers. It involves breaking down the steps of performing a job, identifying hazards at each step, and creating controls to keep workers safe while performing that task. A job safety analysis is sometimes referred to as a job hazard analysis, or JHA.
Risk assessment: A formal process to identify potential hazards related to an activity or operation, analyze the level of risk associated with those hazards, and propose controls to reduce the level of risk. Oftentimes, a risk assessment will use a risk scoring system to assign numerical value to each risk depending on the severity and likelihood it will occur.
So, what’s the difference between job safety analysis and risk assessment?
The key difference between job safety analysis and risk assessment is the scope. Job safety analysis has a much narrower scope, as it involves only job-specific risks. Risk assessment, on the other hand, gives a big picture view of all operational risks including environmental hazards, storm water and waste management, equipment maintenance, and more.
Some other key differences are:
- Who completes each type of assessment?: Job safety analysis is typically completed by the immediate supervisor. The supervisor observes a worker perform the job, and takes notes about potential hazards. By contrast, a risk assessment can be completed by anyone in the organization depending on what it’s for. It can either be a self-assessment, or completed by a third party such as a supervisor or EHS specialist.
- How often are they completed?: There is no specific OSHA requirement for completing a JSA/JHA overall. However, it does provide some guidelines for hazard assessment and PPE selection. Furthermore, organizations can be fined if they don’t protect workers against hazards, so completing a JSA is a good idea. In general, OSHA recommends prioritizing the following types of jobs:
- Jobs with the highest injury or illness rates;
- Jobs with the potential for severe injuries or illness;
- Jobs in which one error could lead to a severe accident;
- New jobs, or those that have undergone changes in processes and procedures;
- Complex enough to require written instructions.
When it comes to risk assessments, you should conduct one any time you identify a hazard or make changes to your operations that could introduce new risks. Since there are so many different types of EHS risk, the timing of EHS risk assessments can vary widely.
Even though job safety analysis and risk assessment are very different, both play an important role in your organization’s EHS risk management strategy.
Examples of job safety analysis and risk assessment
Now that we have a definition for each assessment and understand the differences between them, let’s look at an example of each. Here’s an example of job safety analysis for hitching a tractor and wagon, from the USDA Agricultural Extension:
For each job step, the supervisor has identified potential hazards, and suggested recommended actions to eliminate or control the hazard. The PPE to be worn has also been clearly identified.
You might use a job safety analysis to uncover task-related risks like:
- potential for slips, trips, or falls
- pinch points or places body parts/clothing could get caught in the equipment
- exposure to extreme heat or cold
- loud noises or vibration
- potentially harmful substances or electrical hazards
For comparison, here’s an example of a risk assessment for a poultry farm from Health and Safety Executive:
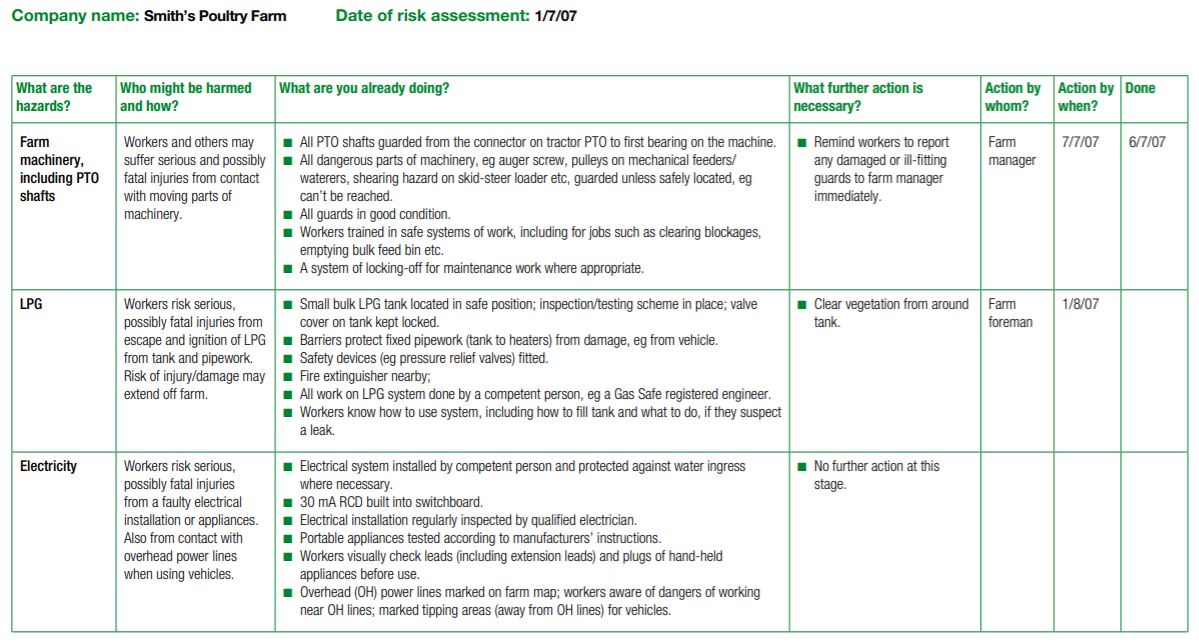
In addition to task-related hazards, the risk assessment identifies potential hazards associated with machinery, chemical storage, electrical systems, building maintenance, and more.
Now that we’ve seen the difference between these risk management tools, let’s take a brief look at how they are different within Perillon.
JSA vs. Risk Assessments in ComplyStation
Lisam’s mobile audit management software gives you the flexibility to perform either type of assessment with one intuitive tool.
Drag and drop questions from a central library to build any form template you need. Add logic to skip questions, generate findings, or trigger corrective actions.
You can also perform assessments on mobile or offline with ComplyStation, so you can capture data, images, and video at the source.
And, Lisam ComplyStation includes risk scoring so you can compare potential hazards and focus your efforts on the most urgent issues.
The bottom line
Job safety analysis and risk assessment, used together in the right ways, can be a powerful combination. Job safety analysis can help you reduce task-specific risks to workers, while risk assessment can help lower your overall corporate risk profile.
Note: This post was originally published in 2017, and has been updated for freshness and accuracy.